Land Drilling
In land drilling, safety padlocks play a critical role in securing equipment, isolating energy sources, and ensuring compliance with OSHA lockout/tagout (LOTO) standards. Deployed on rig components like valves, switches, and access panels, they prevent unauthorized operation during maintenance, minimizing risks of accidental energization. Built with durable materials (stainless steel, composite polymers) to withstand harsh onshore environments—including dust, vibration, and corrosive chemicals—these padlocks integrate with hierarchical keying systems (keyed alike/master keyed) for efficient access control, ensuring worker safety and regulatory adherence in high-stakes drilling operations.
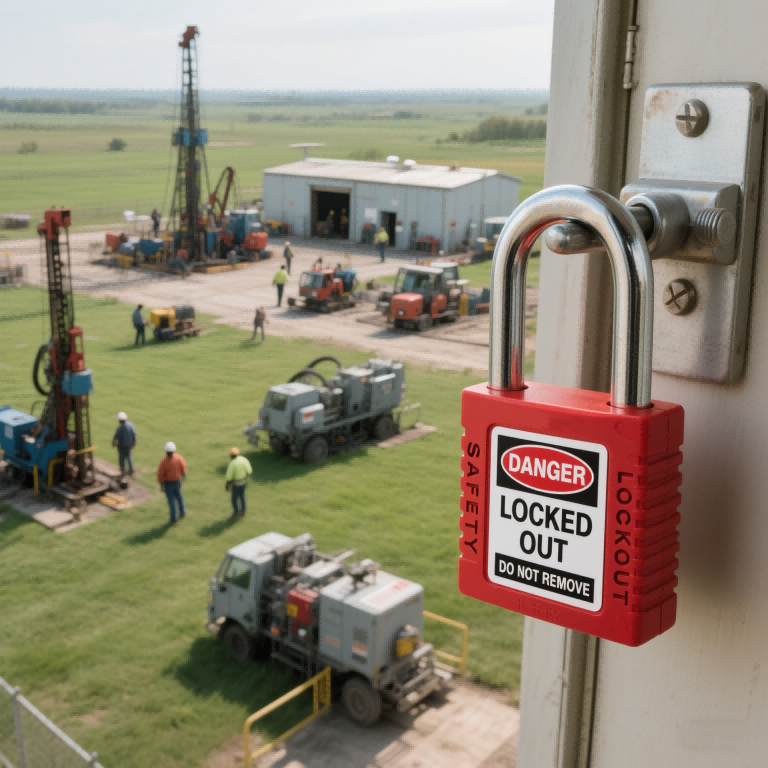
Core Elements of a Lockout Solution
-
Material Selection
>Padlocks
Lock Body: Use impact - resistant and temperature - resistant engineering plastics (such as reinforced nylon PA), which can adapt to extreme temperatures (with a temperature resistance range of - 57℃ to + 177℃). For magnetic - proof and explosion - proof needs, choose insulating materials
Lock Shackle: Prioritize stainless - steel or chrome - plated metal materials, which are highly corrosion - resistant and can withstand moisture, oil, or chemical erosion in drilling sites.
-
Specification and Type Adaptation
>Select padlock specifications according to equipment components. For example, use long - shackle padlocks for large valves or equipment openings, and short - shackle padlocks for small switches or electrical boxes. If there is a lot of dust on - site, choose padlocks with dust - proof designs.
Consider functional features, such as the "key - remaining feature" to prevent the padlock from being left on - site after opening, avoiding misoperation. -
Safety Standards and Certifications
>Ensure that padlocks comply with industrial safety standards (such as OSHA 29 CFR 1910.147), with sufficient strength and durability. Choose products from authorized manufacturers with product certificates. -
Surface Treatment
>Select padlocks with good electroplating quality and uniform coloring. The surface should be free of bubbles and corrosion, with anti - corrosion and anti - oxidation capabilities to extend service life. -
Warning Signs and Readability
>Padlocks should have clear warning signs, such as "DANGER" and "LOCKED OUT", clearly indicating that unauthorized removal is prohibited. Some padlocks should also have writable labels (such as "owner" information) for easy management and traceability.
Steps for Implementing a Lockout Solution (LOTO Procedure)
-
Preparation
Identify all energy sources connected to the machinery or system that requires servicing.
-
Shutdown
Power down the equipment following the proper shutdown procedure for the specific machine or system.
-
Isolation
Physically isolate the machine or equipment from all its energy sources (electrical, mechanical, hydraulic, etc.) using the appropriate lockout devices (e.g., padlocks, valve lockouts).
-
Lockout
Apply lockout devices to all energy-isolating points. Each worker involved in the maintenance should apply their own lock, ensuring multiple levels of protection.
-
Tagout
Attach tags to all locked-out devices, providing clear information about who is responsible for the lockout and the purpose.
-
Release Stored Energy
Safely release any stored energy (e.g., hydraulic pressure, residual electrical energy) in the system to prevent accidental activation.
-
Verification
Verify that the lockout was successful by attempting to operate the machine’s controls to ensure it cannot be energized.
-
Maintenance/Servicing
Perform the required maintenance or servicing while ensuring the lockout remains in place.
-
Re-energizing the Equipment
After the work is completed, verify that all tools and workers are clear from the area. Remove locks in reverse order, with each worker removing their lock only when their part of the work is complete.
-
Restart
Restore energy to the equipment and test it to ensure proper functionality.
Related Products
CUSTOMER CASES
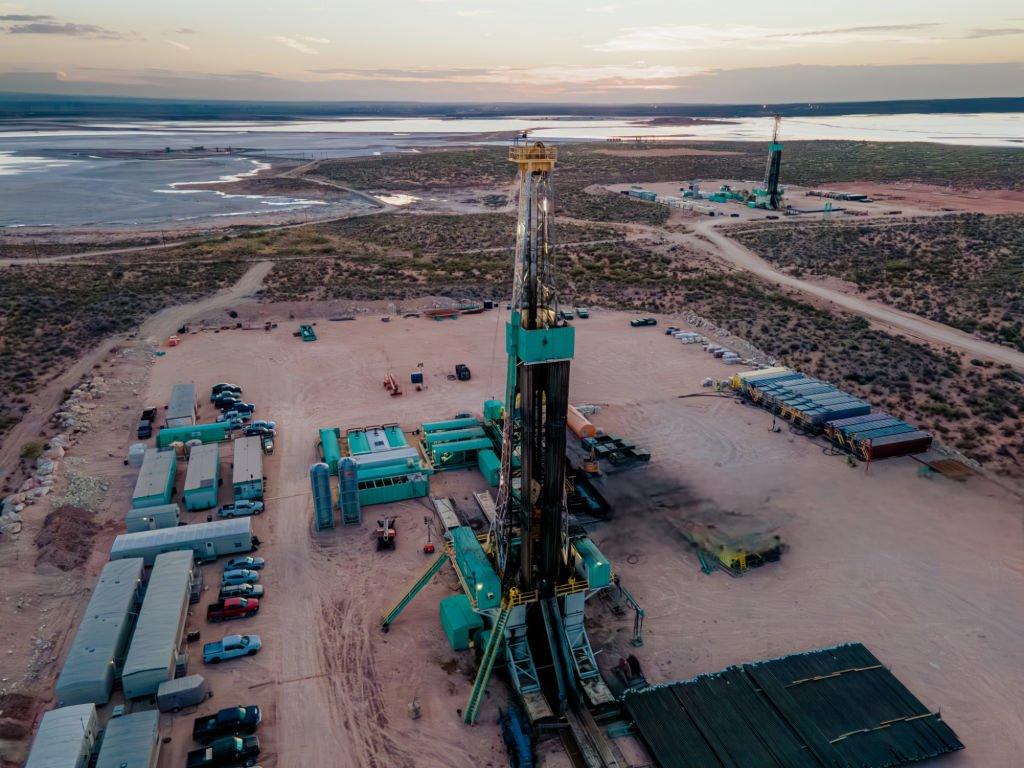
Land Drilling Customer Case
Sendero Drilling, a land - drilling contractor headquartered in San Angelo, Texas, operates primarily in the Permian Basin. By using well - maintained rig fleets and a team of dedicated, trained personnel, they consistently deliver safe and competitive drilling services. For example, in a project involving oil - well drilling in the Permian Basin, Sendero Drilling adhered to strict safety protocols and utilized advanced drilling equipment. This approach not only ensured efficient drilling operations but also met high - industry safety and performance standards, earning trust from clients in the energy sector.
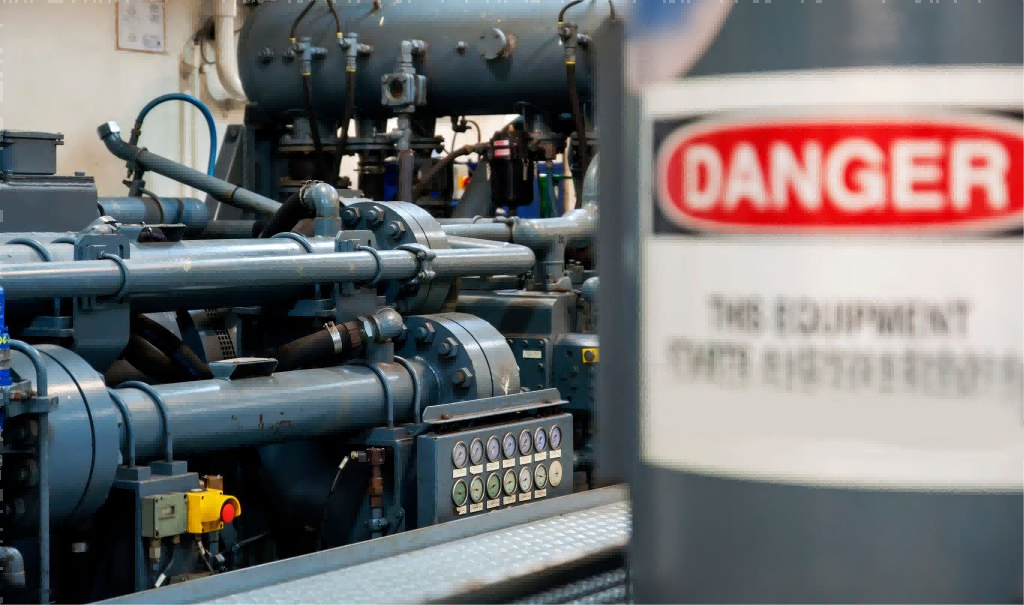
Safety Padlock Customer Case
Automotive Manufacturing Plant Maintenance: In a major automotive manufacturing facility, during assembly - line machinery maintenance, workers employed EPSAFE red safety padlocks (compliant with OSHA 29 CFR 1910.147). These padlocks were used to secure electrical switches and hydraulic - system valves. The padlocks’ durable stainless - steel shackles and clear “DANGER – LOCKED OUT” labeling prevented accidental equipment startup. For instance, when upgrading a robotic welding station, every energy - isolating device was locked out with these padlocks. This ensured technicians could work safely without risk of unexpected power or pressure release, significantly reducing workplace hazards and ensuring compliance with safety regulations.
CUSTOMER REVIEWS
What travelers community are saying.

A***e
⭐ ⭐ ⭐ ⭐ ⭐
I really enjoyed interacting with the supplier. Everything went smoothly and professionally. The products were dispatched and received on time and the quality is impeccable. I would recommend this supplier as they are truly professional and friendly. I didn't experience any problem and I appreciate this smooth transaction.

U***e
⭐ ⭐ ⭐ ⭐ ⭐
Good Quality products. I will order from them again. Good customer service.

J***o
⭐ ⭐ ⭐ ⭐ ⭐
The products they make are of great quality, the customer service is excellent, and everyone is very professional.

K***y
⭐ ⭐ ⭐ ⭐ ⭐
conforme à ma description. je suis très satisfait et recommande vos produits et services


Lockout Solution FAQ
-
What is Lockout/Tagout (LOTO) in land drilling?
-LOTO is a critical safety procedure used to isolate and control energy sources during the servicing, maintenance, or repair of drilling equipment. It prevents unexpected start-up or release of stored energy that could harm workers.
-
Why is LOTO essential in land drilling operations?
+Land drilling rigs involve high-energy, high-risk machinery such as draw works, mud pumps, top drives, and rotary tables. Proper LOTO:
Prevents serious injuries or fatalities
Complies with regulatory standards (e.g., OSHA, IADC)
Protects personnel during non-routine tasks like rig maintenance, breakdown repairs, or rig moves -
What energy sources must be locked out on a land rig?
+Electrical (motors, control panels)
Hydraulic (accumulators, cylinders)
Pneumatic (air-powered tools and controls)
Mechanical (rotating shafts, spring-loaded mechanisms)
Thermal (hot fluids, steam)
Chemical (mud systems, fuel tanks)
Stored Energy (pressure vessels, tension in lines or springs) -
What types of equipment require LOTO in land drilling?
+Top drives and rotary tables
Mud pumps and mixing tanks
Pipe handling systems
Blowout preventer (BOP) control units
Centrifugal and triplex pumps
Generators and electrical control panels
Air compressors and hydraulic systems -
Who is authorized to perform LOTO on a drilling rig?
+Only authorized personnel who have received LOTO training are permitted to apply or remove lockout devices. Other crew members must be considered affected personnel and should be made aware when LOTO is in effect.
-
What is the procedure for applying LOTO in land drilling?
+1.Notify all affected crew.
2.Shut down equipment using standard procedures.
3.Isolate all applicable energy sources.
4.Apply lockout devices and tags at each isolation point.
5.Release stored energy (bleed off pressure, drain fluids).
6.Verify isolation before beginning any work. -
What special considerations apply to LOTO on a rig?
+Equipment is often interconnected, so all energy sources must be carefully traced and isolated.
Rigs may have multiple crews or contractors—clear communication and a group lockout system is critical.
Environmental conditions (dust, rain, heat) may require durable lockout devices. -
How is LOTO handled during crew or shift changes?
+A formal shift change LOTO transfer procedure must be followed:
Outgoing workers remove their locks only after confirming incoming workers apply their own.
No energy source may be re-energized between shifts. -
What devices are used for LOTO on a land rig?
+Padlocks (keyed individually for each worker)
Hasps for group lockout
Valve and breaker locks
Tagout tags with employee details
Lockout boxes for central management during complex operations -
Is LOTO mandatory under regulations?
+Yes. In the U.S., LOTO is required by OSHA 29 CFR 1910.147. Internationally, compliance with standards such as IADC safety guidelines, ISO 45001, and company HSE policies is expected.