Chemical Refining
Secure valves on pipelines (e.g., hydrocarbon feedstock, acid catalysts) to prevent unintended flow during valve maintenance.
Lock electrical disconnects, pump controls, and reactor agitators to eliminate risks of mechanical motion or electrical arcs.
Isolate storage tanks (e.g., volatile solvents, corrosive acids) via padlocked manway covers or transfer lines.
Critical Equipment:
Refinery columns (distillation, fractionation), heat exchangers, and compressor stations during inspection or repair.
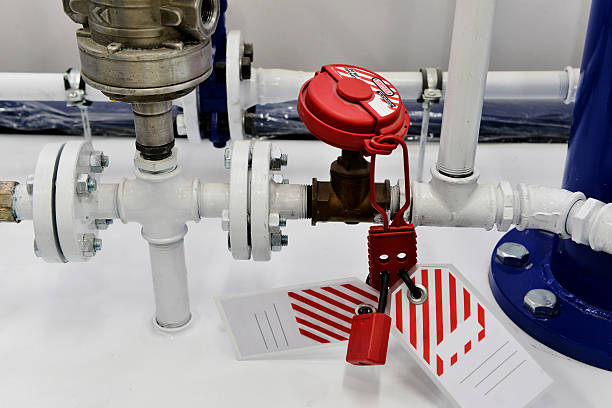
Core Elements of a Lockout Solution
-
Unintended Energy Release
>h4>PadlocksInadequate isolation of power (motors, control circuits), pressure sources (pumps, compressors), or heat (heaters, reactors) during maintenance, leading to mechanical injuries, burns, or chemical leaks.
Valve Lockouts
Circuit Breaker Lockouts
Circuit Breaker Lockouts
Plug and Electrical Lockouts
Pneumatic and Hydraulic Lockouts
Cable Lockouts
-
Energy Isolation Point Analysis & Padlock Selection
>h4>PadlocksElectrical Systems: Circuit breakers, switchgear, motor starters (secured with circuit breaker locks and switch locks paired with safety padlocks).
Valve Lockouts
Circuit Breaker Lockouts
Circuit Breaker Lockouts
Plug and Electrical Lockouts
Pneumatic and Hydraulic Lockouts
Cable Lockouts
-
Fluid Systems
>Padlocks
Valves (ball, gate, globe valves), blind flanges, hose connections (using valve locks, blind flange locks, and pipe clamps with corrosion-resistant padlocks).
Valve Lockouts
Circuit Breaker Lockouts
Circuit Breaker Lockouts
Plug and Electrical Lockouts
Pneumatic and Hydraulic Lockouts
Cable Lockouts
-
Mechanical Systems
>Padlocks
Couplings, pulleys, flywheels (protected by mechanical lock covers or interlock systems).
Valve Lockouts
Circuit Breaker Lockouts
Circuit Breaker Lockouts
Plug and Electrical Lockouts
Pneumatic and Hydraulic Lockouts
Cable Lockouts
-
Thermal/Pressure Systems
>Padlocks
Steam valves, pressure vessel relief valves (locked in the open position to prevent pressure buildup).
Valve Lockouts
Circuit Breaker Lockouts
Circuit Breaker Lockouts
Plug and Electrical Lockouts
Pneumatic and Hydraulic Lockouts
Cable Lockouts
Steps for Implementing a Lockout Solution (LOTO Procedure)
-
Preparation
Identify all energy sources connected to the machinery or system that requires servicing.
-
Shutdown
Power down the equipment following the proper shutdown procedure for the specific machine or system.
-
Isolation
Physically isolate the machine or equipment from all its energy sources (electrical, mechanical, hydraulic, etc.) using the appropriate lockout devices (e.g., padlocks, valve lockouts).
-
Lockout
Apply lockout devices to all energy-isolating points. Each worker involved in the maintenance should apply their own lock, ensuring multiple levels of protection.
-
Tagout
Attach tags to all locked-out devices, providing clear information about who is responsible for the lockout and the purpose.
-
Release Stored Energy
Safely release any stored energy (e.g., hydraulic pressure, residual electrical energy) in the system to prevent accidental activation.
-
Verification
Verify that the lockout was successful by attempting to operate the machine’s controls to ensure it cannot be energized.
-
Maintenance/Servicing
Perform the required maintenance or servicing while ensuring the lockout remains in place.
-
Re-energizing the Equipment
After the work is completed, verify that all tools and workers are clear from the area. Remove locks in reverse order, with each worker removing their lock only when their part of the work is complete.
-
Restart
Restore energy to the equipment and test it to ensure proper functionality.
CUSTOMER CASES
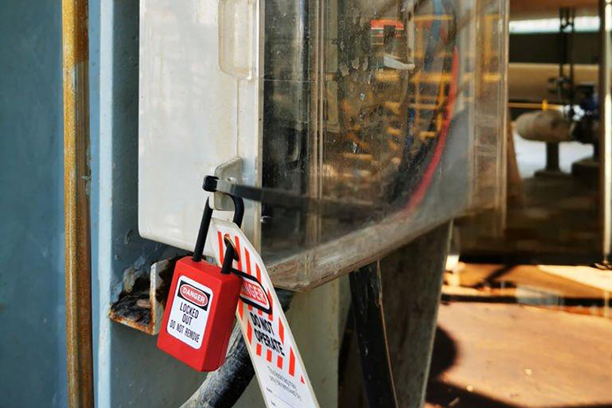
Chemical Refining & Safety Padlock Solutions
1. ExxonMobil Baton Rouge Refinery (USA)Industry: Oil refining and petrochemicals Challenge:
High-risk maintenance operations on distillation columns, reactors, and pipeline systems exposed workers to chemical leaks, pressure surges, and unexpected energy releases.
Multi-team collaboration (e.g., process engineers, electricians, contractors) led to miscommunication and unauthorized equipment restarts.
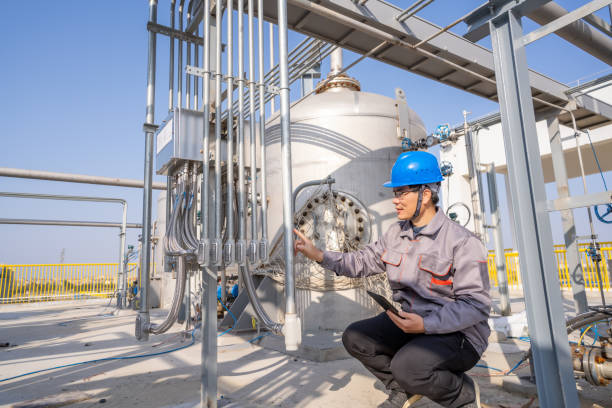
LOTO System Upgrade Practice of a Petrochemical Enterprise
I. Customer Background
A large - scale petrochemical enterprise (hereinafter referred to as "XYZ Petrochemical") is a leading oil refining and chemical production base in China. It has refining units capable of processing 30 million tons of crude oil annually, covering core process units such as atmospheric and vacuum distillation, catalytic cracking, hydrofining, and ethylene cracking. There are over 200,000 kilometers of high - temperature and high - pressure pipelines, more than 5,000 dynamic equipment (pumps, compressors), and over 100,000 electrical control boxes and valves in the plant area. In 2022, two minor leakage accidents caused by unexpected equipment startups exposed the shortcomings of the existing Lockout/Tagout (LOTO) system in terms of adaptability to corrosive environments, multi - team collaboration management, and compliance traceability.
CUSTOMER REVIEWS
What travelers community are saying.

A***e
⭐ ⭐ ⭐ ⭐ ⭐
I really enjoyed interacting with the supplier. Everything went smoothly and professionally. The products were dispatched and received on time and the quality is impeccable. I would recommend this supplier as they are truly professional and friendly. I didn't experience any problem and I appreciate this smooth transaction.

U***e
⭐ ⭐ ⭐ ⭐ ⭐
Good Quality products. I will order from them again. Good customer service.

J***o
⭐ ⭐ ⭐ ⭐ ⭐
The products they make are of great quality, the customer service is excellent, and everyone is very professional.

K***y
⭐ ⭐ ⭐ ⭐ ⭐
conforme à ma description. je suis très satisfait et recommande vos produits et services


Lockout Solution FAQ
-
Which safety standards apply to lockout solutions in chemical refining?
-Key standards include:
OSHA 1910.147 (USA): Mandates energy isolation, employee training, and verification of zero energy before work.
ISO 45001 (Global): Requires systematic hazard control, including LOTO, for occupational health and safety.
API Standards (e.g., API 700): Specifies lockout hardware requirements for petroleum and chemical equipment.
Local Regulations: E.g., China’s GB/T 33579 for lockout/tagout in industrial maintenance. -
How do I choose the right safety padlocks for corrosive chemical environments?
+Select based on:
Material Compatibility:
Stainless Steel 316: For acids (e.g., sulfuric acid), alkalis, and saltwater (common in coastal refineries).
Nylon/Plastic: Non-conductive, ideal for electrical panels or non-corrosive but moisture-rich environments (IP67/IP68 rating for dust/water resistance).
Hot-Dipped Galvanized Steel: Suitable for moderate corrosion (e.g., mild alkaline solutions), but avoid in strong oxidizing agents.
Design Features: Full-enclosed shackles (防切割 / 防卡塞), large identification plates for labeling, and compatibility with isolation devices (e.g., valve locks, breaker switches). -
What are the core steps to implement a lockout solution in a refinery?
+Energy Source Identification: Catalog all energy types (electrical, hydraulic, thermal, chemical) and isolation points (valves, switches, breakers).
Hardware Selection: Deploy safety padlocks, valve locks, blind flange locks, and hasps tailored to equipment and environment.
Procedure Development:
Shutdown equipment per manufacturer guidelines.
Isolate energy sources and apply locks/tags (one worker = one unique padlock).
Verify zero energy (e.g., voltage testing, pressure gauging) before work. -
How to manage lockout during multi-team maintenance (e.g., process, electrical, instrumentation teams)?
+Multi-Lock Hasp System: Use a shared hasp to allow multiple padlocks on a single isolation point (e.g., a reactor feed valve). Each team locks with their padlock; equipment restarts only when all locks are removed.
Digital Coordination Tools: Software (e.g., Brady Link360, Enablon) to track lock status, assign permissions, and ensure all stakeholders confirm isolation.
Clear Accountability: Each worker uses their personal padlock; no shared keys to avoid unauthorized removal. -
What if a lockout device fails (e.g., rusted padlock, incompatible valve lock)?
+Preventive Maintenance: Inspect locks quarterly for corrosion, shackle movement, or damage. Replace padlocks every 2–3 years (sooner in harsh environments).
Redundancy: Use dual isolation (e.g., lock + tag) for critical points or add blind flanges for high-risk fluid systems.
Emergency Protocols: Have a dedicated toolkit for removing failed locks (e.g., bolt cutters for emergency situations), followed by immediate replacement and root-cause analysis. -
Can tagout (tagging without locking) replace padlock lockout in chemical refining?
+Lockout is Preferred: OSHA and industry standards prioritize physical lockout for reliability, as tags alone can be ignored or misinterpreted.
Tagout Use Cases: Only permissible when lockout is infeasible (e.g., no lockout - compatible isolation device), but requires written justification, enhanced warnings, and immediate lockout when devices become available. -
How to train workers on lockout procedures in high-risk refining environments?
+Hierarchical Training:
Authorized Workers: Hands-on training on lock selection, application, and energy verification (including live simulations of voltage/pressure checks).
Affected Workers: Education on lockout boundaries, risks of tampering, and communication protocols with authorized personnel.
Scenario-Based Drills: Simulate emergencies (e.g., accidental startup during maintenance, chemical leaks) to test response.
Certification: Require annual re-training and document competency (e.g., OSHA - compliant certificates). -
How to integrate digital tools into a lockout solution for better traceability?
+QR Codes/NFC Tags: Link padlocks to digital records for real-time tracking of lock location, user, and timestamp (e.g., scan to view isolation point details and approval status).
Mobile Apps: Enable workers to log lockout steps, upload verification photos, and receive alerts for expired locks or missing isolations.
Centralized Database: Maintain a digital 台账 of all lockout events, inspections, and deviations for audit readiness (e.g., compliance with ISO 45001 documentation requirements). -
How to handle emergency situations (e.g., fire, leak) requiring bypass of lockout?
+Emergency Unlocking Protocol:
Authorized supervisors approve bypass after notifying all workers and documenting the reason (e.g., life - threat).
Use a dedicated "emergency key" (controlled by security/safety teams, requiring dual signatures for release).
Re - apply lockout immediately after the emergency and conduct a post - incident review.
Post - Emergency Actions: Retrain involved personnel, update procedures if gaps are found, and report the incident to safety committees. -
Are there industry - specific lockout solutions for refining equipment like distillation columns or reactors?
+Distillation Columns: Lock cooling water valves (prevent thermal shock) and steam inlet valves (use double - lock hasps for multi - team accountability).
Reactors: Isolate feed valves, lock agitator motor circuits, and secure 泄压 valves in the open position during maintenance.
Pumps/Compressors: Lock power switches and inlet/outlet valves to prevent backflow or accidental motor startup.